
In our quest to learn everything there is to know about traction and tires we’ve always been curious what the athlete testing portion of the story entails. How and where do athletes go to push prototypes to their limits before they are willing to try them in a real race scenario?
We called up multi-time EWS and DH champion Fabien Barel who is currently working with Pirelli to develop a full line of gravity race tires for the legendary Italian Formula 1 brand. In the past, Barel partnered with Michelin for six years to create their current gravity tire lineup, and he has been working with Canyon for almost ten years now, both racing and testing frames and now running their gravity team. It’s safe to say he knows a few things about riding prototypes and providing feedback.
To get started, Barel says he tested every tire in the Pirelli MTB range to learn where the brand is at and what’s possible. He considered the three main aspects of each tire: casing, rubber compound, and tread pattern. Barel says that they analyze each of those tire components individually until they are dialed, then move on to the next and consider how they overlap and interact with one another. For example, he says that the damping qualities of the rubber will also work with the damping of the casing, so everything has to play well together to create the desired grip, support, and puncture protection.
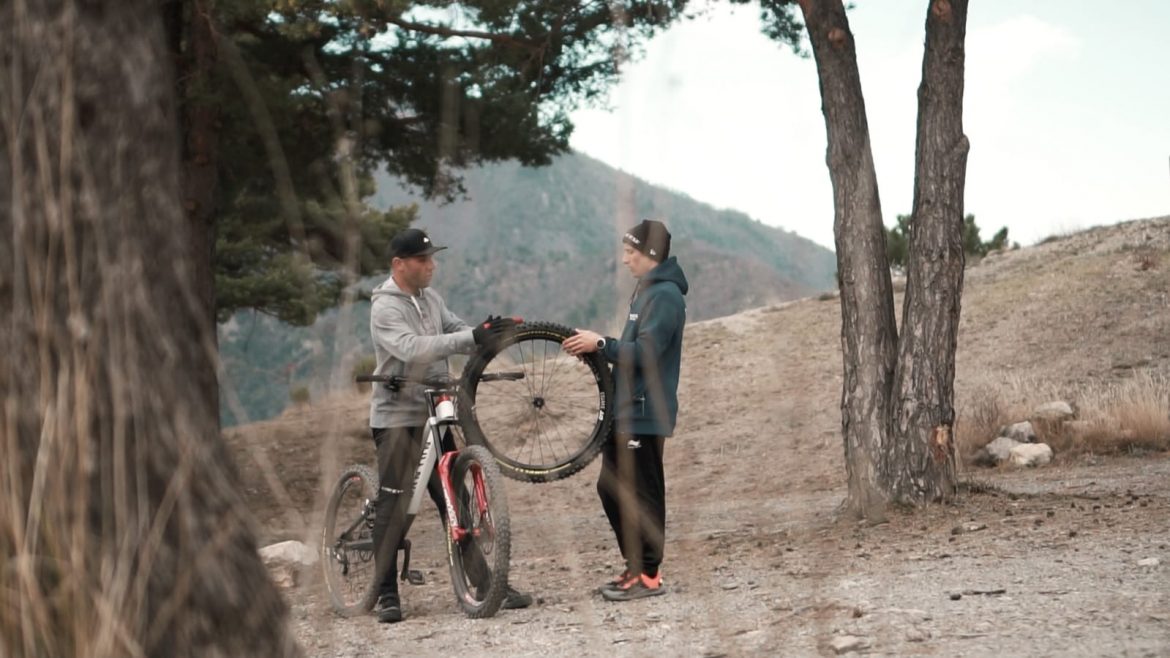
Barel lives in Nice, France, where he can test frames and tires on some notably loose and rocky trails. He also has access to legendary DH tracks in Sanremo, Italy, with longer and steeper options not far off in the Alps. While he does meet the Pirelli engineers in other locations, those three spots provide a good variety of terrain and weather variation to see how the products perform. There are several average riders and some EWS racers involved in the testing as well, and their perspectives help the brand gain a broader perspective of how the tires will work for their customers. Not every rubber engineer or product designer at Pirelli is a mountain biker, so the information they receive from riders is invaluable. It’s likely none of the engineers has driven a Formula 1 car either, but they make tires for the entire race field based on driver feedback.
All of the initial prototype tires use a wire bead to give them the best lock with the wheel so they can be pushed as hard as possible, and the folding tires will be designed next. Barel likened it to frame testing. “When you develop a bike, you develop the race machine and then you bring it down for the customer usage. I would say that the wire bead is the race machine, and once you’re there you know that you’ve got to bring it slowly down to a foldable; to be lighter and more acceptable for an average user.” He considers three factors in terms of the casing, including the weight, deformation for grip and comfort, and the puncture resistance and support. He says that tires above 1,500g are often considered too heavy for DH, and more than 1,300g is thought to be too heavy for enduro racing, so they need to stay below those numbers to compete in the market.
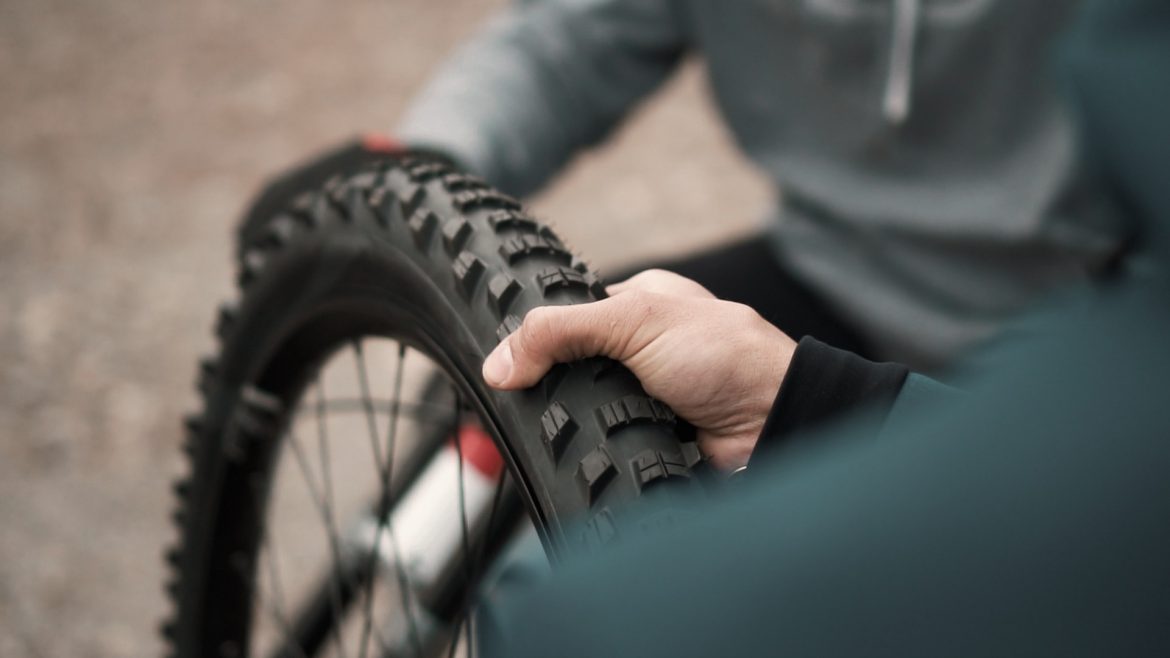
Since the gravity tires will be used by consumers on enduro race bikes and their e-bike counterparts as well as downhill sleds, he tests the tires with all three options. Barel said that they are primarily using alloy rims with 28-30mm internal widths and that the tire pressures are kept at a consistent measurement to eliminate variables. He also doesn’t adjust suspension between tests, keeping the tune where he would want it with a good tire that he already trusts and comparing the prototypes accordingly. The aim is to make these tires puncture-resistant without the use of inserts, so they are not currently testing with any foam between the tire and rim. There are always a few reference tires from other brands in the mix to compare and contrast, with the goal of creating a better grip than the competition. The test day consists of back-to-back runs at a consistent speed, swapping tires, and taking notes throughout.
Due to the differences in lateral stiffness and radial compliance between aluminum and carbon fiber rims Barel says that they will conduct completely separate tests between the two materials. “When you move to carbon wheels you increase lateral rigidity, so that’s something you have to consider in your construction. There are probably some tires that will be advised for alloy wheels while some others will be clearly specified for carbon. This will come on the market from every brand, I imagine. [For carbon] you need to reinforce the beads on the tire because a carbon rim provides a lot more lateral rigidity than alloy. And you need to find a way to have more frontal comfort because the carbon provides more feedback in the pedals and the handlebar. So laterally you need to add rigidity to the casing to not have the tire rolling, and [radially] you need to gain comfort and avoid vibration, which is not super easy to make, to be honest.”
Instead of simply looking for maximum grip, Barel says that his main aim is to create a tire that’s more controllable when you lose grip. Losing traction is inevitable, and it can either happen suddenly, throwing the bike off line or causing a crash, or traction can be lost in a predictable manner where the rider can feel it and adjust their weight to maintain grip. This controllable situation is what Barel and Pirelli are aiming for, and he says that a lot of that control is effected by the transition between shoulder and center knobs as the tire is leaned into a turn. The space between those knobs and the profile of the tire are two of the factors they can play with to find a balanced and hopefully confidence-inspiring tread.
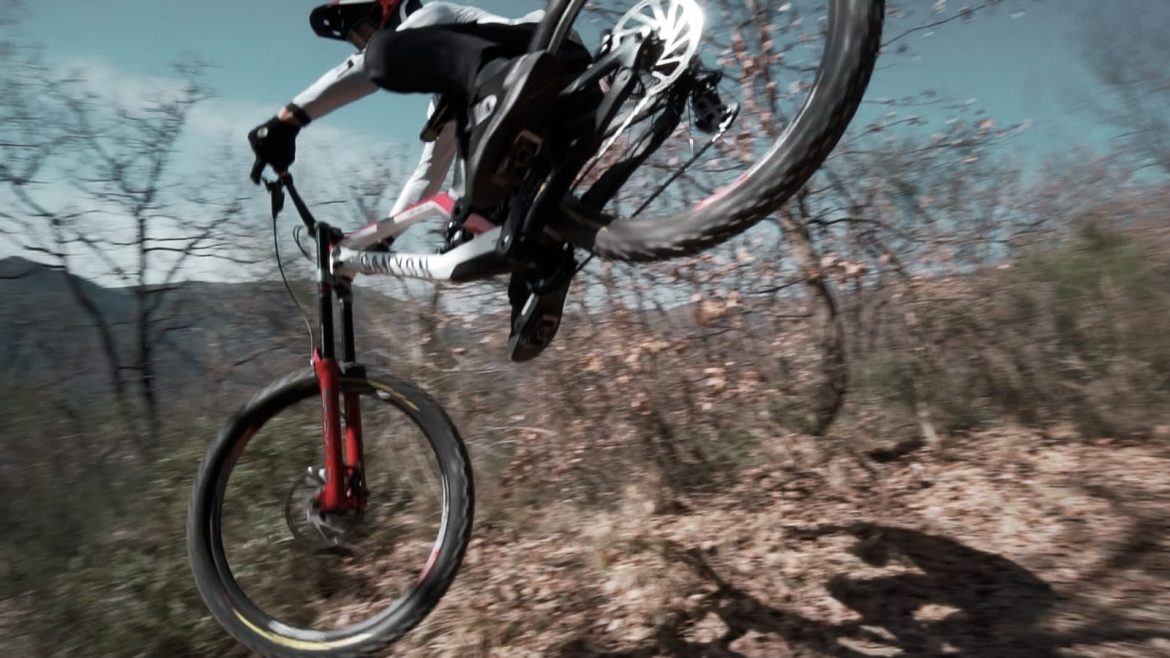
From my perspective, a good tire is not necessarily a tire that’s got the highest grip point. For me the most interesting tire is the one where you feel that you’re losing the grip, so you can anticipate your movement to actually control the bike and not fall. I’d rather have slightly less grip, and feel the grip going away than have more grip and when I lose it I go right to the floor. Because it makes the rider’s confidence higher. So that’s what we’re working on. This comes 20-30% from the casing, and then [the rest] will come from the tread pattern and rubber quality.
We asked bout any major flops or failures with prototype tires in testing, and Barel says that so far things have been going really well. He did mention one mold prototype where the center tread was too tall, compared to the shoulder lugs, making it very difficult to confidently lean the tread into a turn.
Finally, we asked Barel specifically about tire profile, and he confirmed that a relatively square profile with a close transition between the central and shoulder knobs, combined with a good amount of overall elasticity, creates the confidence to dip the bike deep into the turn and use the full advantage of the larger shoulder knobs. Two tires he mentioned as industry benchmarks in terms of profile and lean-factor are the Schwalbe Magic Mary and Maxxis Assegai, both well-loved by racers for their all-conditions cornering capabilities.
In terms of tread, Barel mentioned that they are working on a spectrum from purely dry condition tires that roll fast to genuine mud spikes, and likely some rear-specific patterns. The current idea is that this research and design phase will result in three to four new gravity tires in the Pirelli line over the next two years.
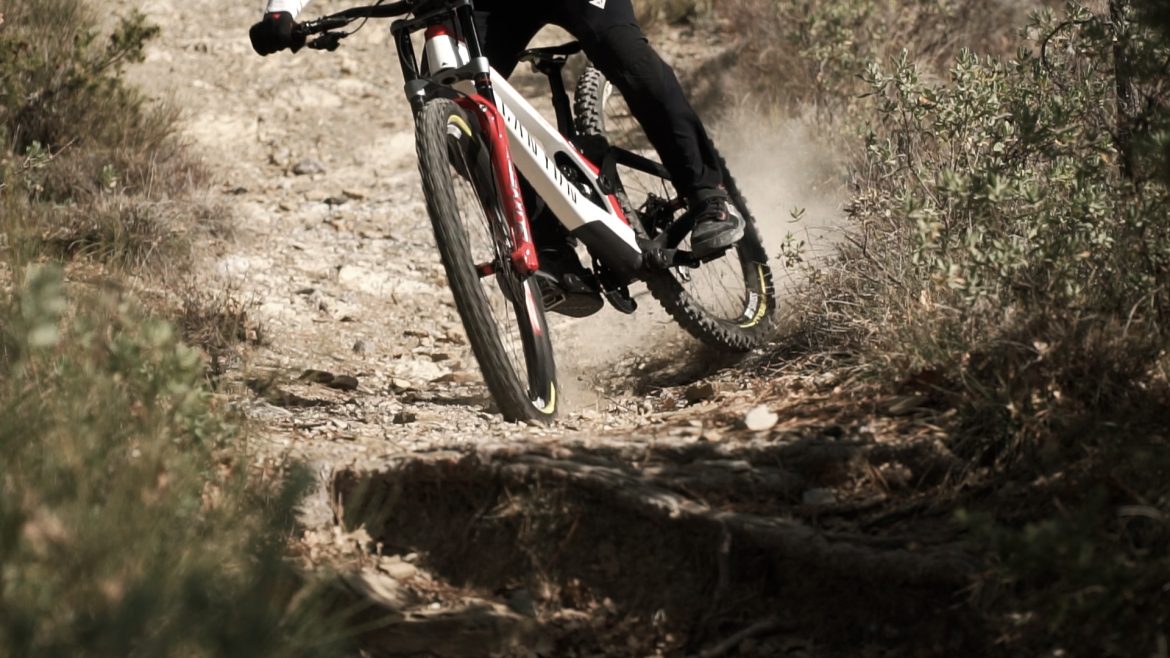
While Pirelli has a long history of making tires for dirt and asphalt use, Barel says that they do test the extremes of carcass weight and tread compound to find where the limits are for mountain bikes. Testing tread compounds and casing layups is quite common, but the tread pattern itself is the harder element because the molds to create them are quite expensive. The pattern itself is closely scrutinized to make sure that changes to the prototype are necessary and likely to yield benefits.
Once you find a compromise that works you always try to go further one way or the other to make sure that it’s actually the sweet spot. There’s a lot of knowledge in tires that allow us to have fairly rational and objective development. But the last 20%, the choice and the character you give a tire, is often subjective decisions based on instinct and what you can feel. I guess that’s where Pirelli trusts me.
Pirelli is currently building a new factory in Milan, where they will be crafting these tires in the future. Not only will the home base allow for a smaller carbon footprint, but they will have full control of supply moving forward.
0 Comments