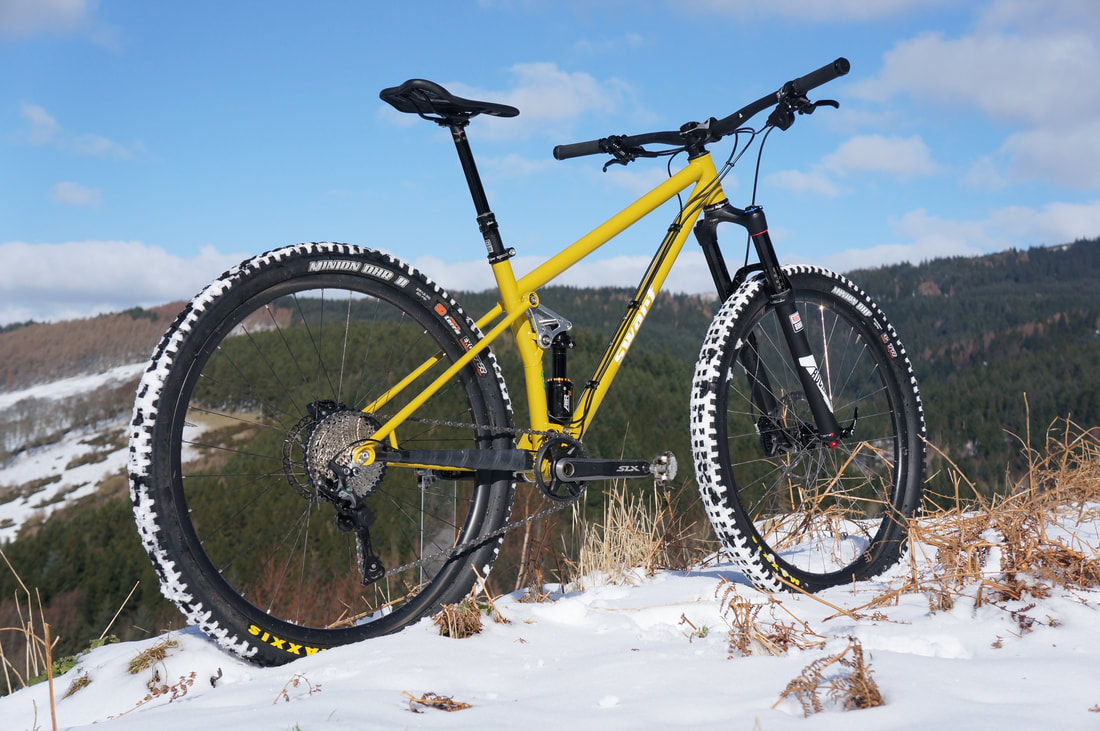
Photo: Swarf Cycles
With numerous steel full suspension frame models on the European market and myriad fully-custom configurations, we wanted to sit down with several builders and ask why they chose the carbon and iron-based alloy rather than carbon fiber, aluminum, titanium, magnesium, or bamboo.
I can’t say if it’s the clean lines drawn from round tubes or the fact that you can see where human energy formed them, but steel bikes are sexy. Their sharp angles often establish an unspoiled mountain bike silhouette, free of aero or hydrodynamic considerations. Fortunately, it’s not all about form, and there is a great deal of functional value to steel frame manufacturing.
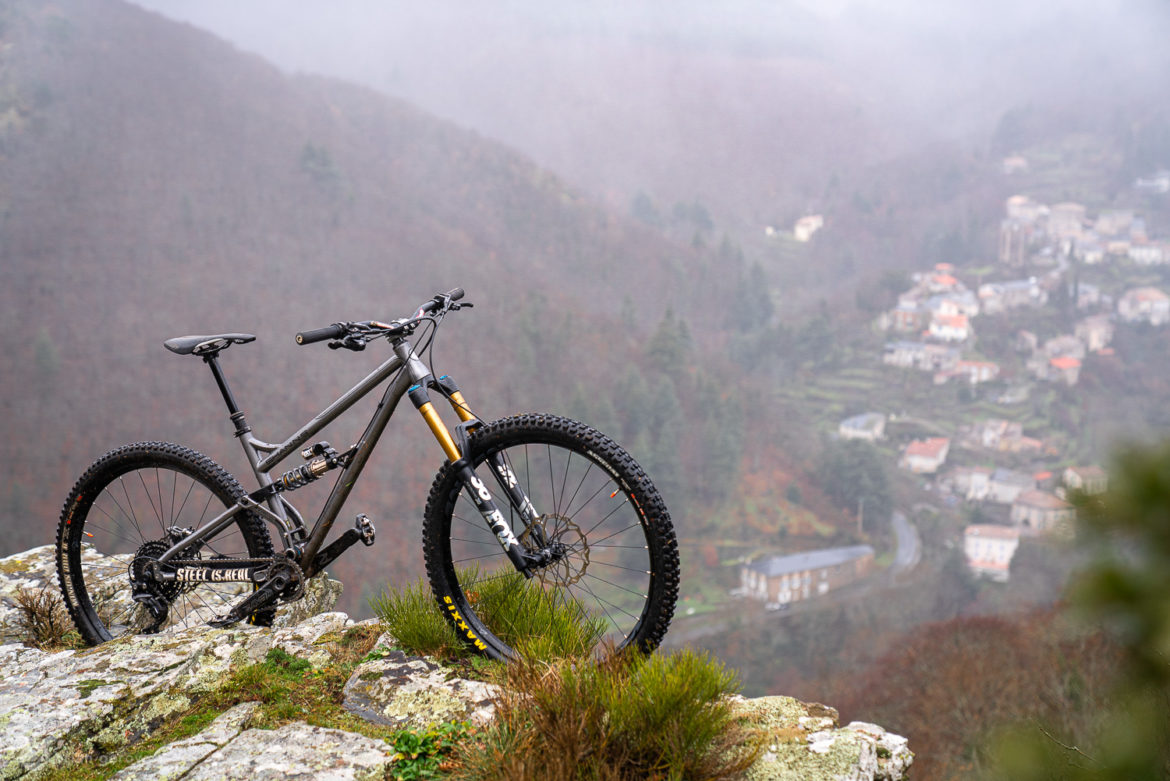
Steel affords frame builders the ability to easily add cage mounts and shift geometry angles to fit their engineering and aesthetic desires. If a client wants a bike with a 5mm shorter reach measurement, they can simply chop the tubes shorter. For tall riders, builders can use thicker tubing to stiffen the bike and improve its ride characteristics, and shorter folks can have a frame that genuinely fits and functions as it should. While alloy and carbon frames can be modified and customized, steel is the most forgiving and malleable mountain bike frame material currently in use.
The seven frame builders we chatted with all have their own reasoning and theories behind steel tubing, and their bikes all share a few common threads. Each of them employs a decidedly simple single-pivot suspension design, and they’re all mid- to longer-travel bikes designed with descending as a primary objective. Most of the builders also make or design hardtails and other frames, but we’ll be focusing on their squishy options below.
Who started the squishy steel party anyway?
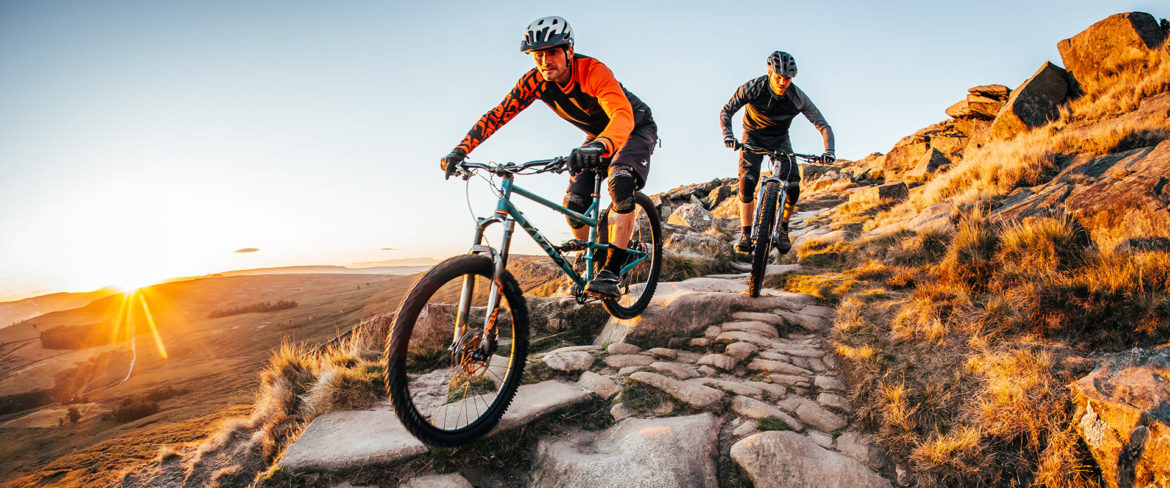
Though steel bike frames have been around longer than any other collection of tubes, this modern iteration of full sus whips has a particular origin. For several reasons that we’ll discuss later, the lion’s share of current frame builders reside in England. Cotic Cycles was the first UK builder to offer a contemporary steel dual suspension bike, with their Rocket26 model that debuted in 2012. The bike was previously released in aluminum and Cotic owner, Cy Turner, was on the hunt for a way to stiffen up the connection between the front and rear triangles.
In terms of steel’s stiffness characteristics, Cy says, “Aluminium gets its stiffness in bikes from being light enough to use big [tubing] sections, so the size of the tube gives it stiffness. When the tubes are the same diameter (like a 35mm seat tube) despite differing wall thickness, steel is intrinsically 3x stiffer than aluminum, so without section size to do its job for the aluminum I found a steel seat tube would be a great keystone to a full suspension frame, and it all developed from there.”
Cy mentioned that the full suspension bikes he builds come from a tradition of talented UK welders making steel hardtails that would hold up to the island nation’s consistent dampness better than any bike full of pivots.
“The UK has pretty inclement weather at times, but it’s not that cold and it doesn’t snow, so we tend to ride all year round in quite wet conditions through the winter. Early full suspension bikes just dissolved in these conditions, but people wanted big tires, good brakes and good geometry for their bikes, so a bunch of British brands sprung up offering progressive, tough, steel hardtails that would withstand our winters. As time has gone on the whole industry is better at designing long-lived full suspension bikes, but we were the first British brand to make the jump into steel full suspension. ”
The DIY-ability of steel makes it an approachable material
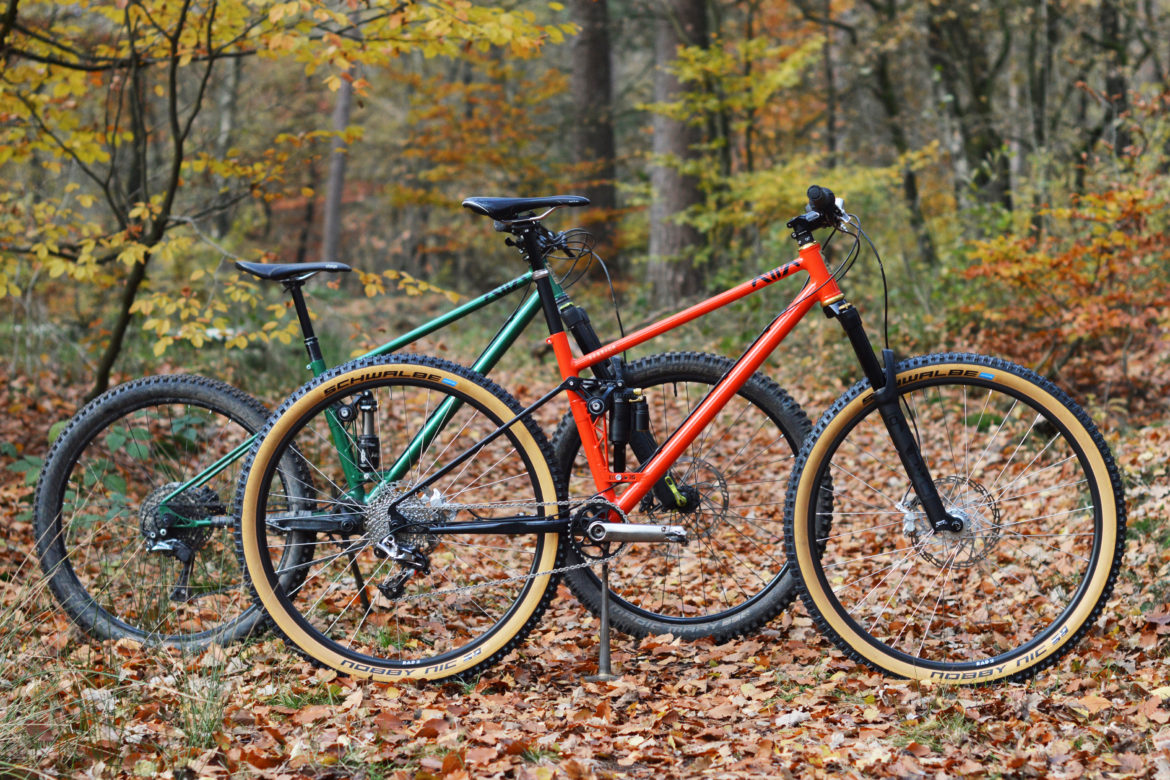
Nearly all of the frame builders we got in touch with noted “doability” as a factor in their choice to work with steel tubes. To build with steel you need cutting and shaping tools, appropriate welding gear, and a frame jig of some sort. You can do all of the work in a garage or ventilated basement, and there is a high likelihood that your very first prototype can be a rideable one if you follow some instruction. With titanium, you would need a near surgically sanitary working space, aluminum takes longer to learn how to weld properly, and a single size carbon-fiber mold can cost more than two American kids’ first college degrees.
In addition to the DIY-ability of the material, termed the “guys in shreds factor” by more than one UK builder, several frame fabricators mentioned the quality and proximity of Reynolds tubing as a possible contributor to the number of steel bikes made or designed in the UK. Reynolds has been around since 1897 when “Alfred M. Reynolds and J.T Hewitt patented the invention of butted tubing.” Their innovations have continued to benefit bikes in a number of ways over the past 123 years, and they now also produce steel and titanium tubing for use outside the cycling sector.
Steel performance: Flexibility, rigidity, repairability, and overall durability
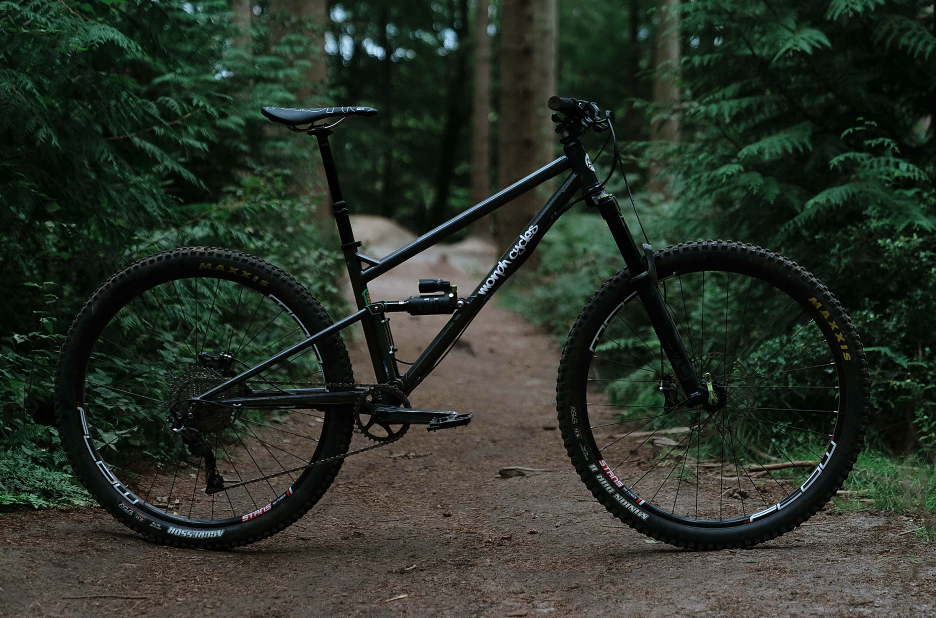
So, why steel? Cy touched on this a bit earlier and adds that “I use steel for performance. I use it on the droplink full suspension bikes for the same reasons I use it on the hardtails and gravel bikes: Steel is tough, durable and gives our bikes their beautifully clean lines. Because of its incredible strength, it allows me to use it in relatively thin sections when designing the frames, which gives the bikes outstanding ride feel. Using steel gives our hardtail and full suspension frames a gorgeous, tactile, and traction-enhancing flex along the length of the bike, allowing them to breathe with the trail instead of fighting it.” You can read the full steel manifesto on the Cotic website, along with a helpful example of how the material affects suspension efforts in certain situations.
Michiel Burgerhout of Project12 Cycles in Holland shared his appreciation for the adaptability and selection of steel tubing sizes and thicknesses.
“With steel, you have a very broad range of customizable tube sets. If you go to carbon or aluminum, it’s a bit harder to get the nice stuff. I build custom, and steel is a very logical choice. It also rides nicer than any other material I know. But you have to use the right tubing. I’ve ridden steel frames that were as harsh as the harshest aluminum frames, and some that were soft or sloppy.”
Alan Finlay of Pipedream Cycles speaks to the “steel is real” hashtaggeers a bit.
“Ride sensation is mentioned a lot and this might be relevant when describing a road bike or hardtail mountain bike frame, especially when there are few other differentiators between one frame or another. However, there are so many other factors that determine how a bike ‘feels’ — wheels would be one of them,” says Finlay.
“Personally, I think a lot of our vocabulary or terminology with respect to steel (or titanium, for that matter) comes from the last century: we’re using the same descriptives — perhaps rooted in our romance with the material, or nostalgia — for a material that has been developed into something really special. The steel ‘superalloys’ really are incredible and the fabricators and welders who work with the material are craftsmen. In their hands, it’s possible to create a bespoke frame with unique characteristics and that elusive ‘steel is real’ quality if that’s what you want. If you’re building a frame in larger quantities, the design and specification needs to work for a wide spectrum of riders. All that to say, an ‘off the peg’ steel frame might feel different to two riders who may be the same height but differ in weight by as much as 50lbs.”
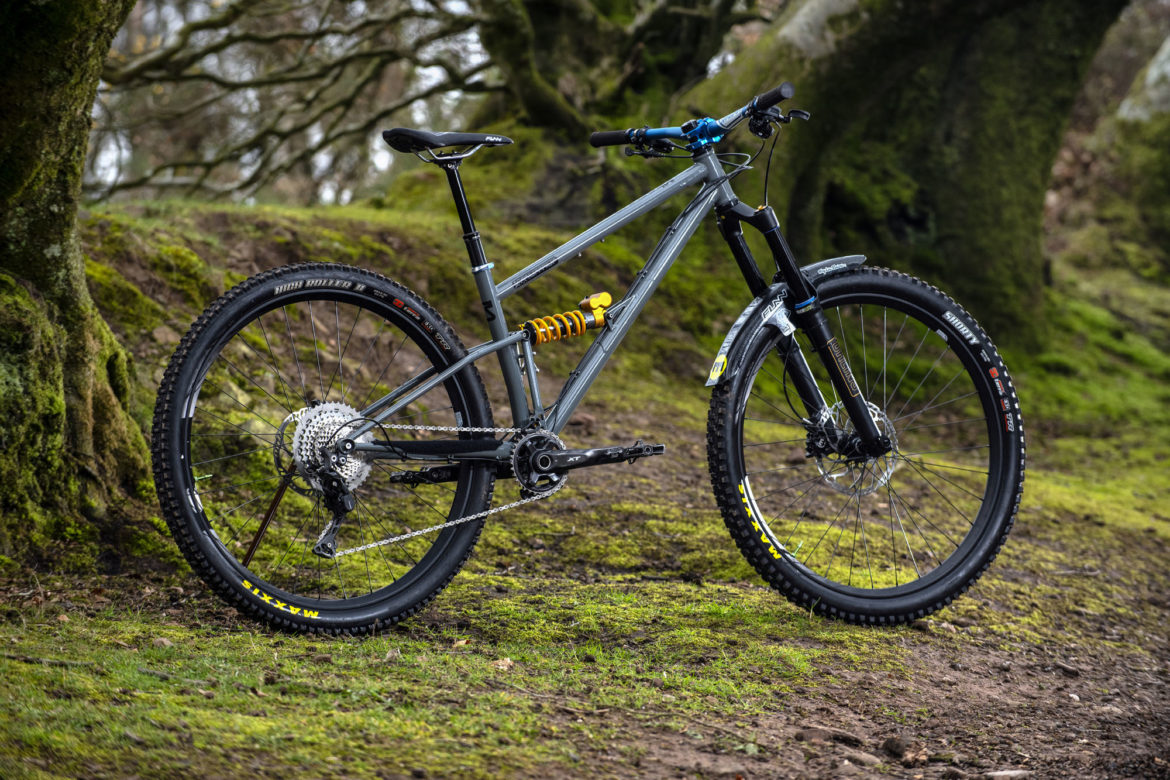
There’s also an important availability factor.
“Here in the UK, getting ahold of aluminum tubing in the sizes and shapes is more difficult than it is in, like the far east for example,” says Paul Burford of BTR Cycleworks. “Then the aluminum tubes need to be heat-treated after they’re welded, so that adds another process and another cost.” Buford started off making hardtail DH frames, and currently builds nine different hardtail models in addition to his Pinner full sus bike.
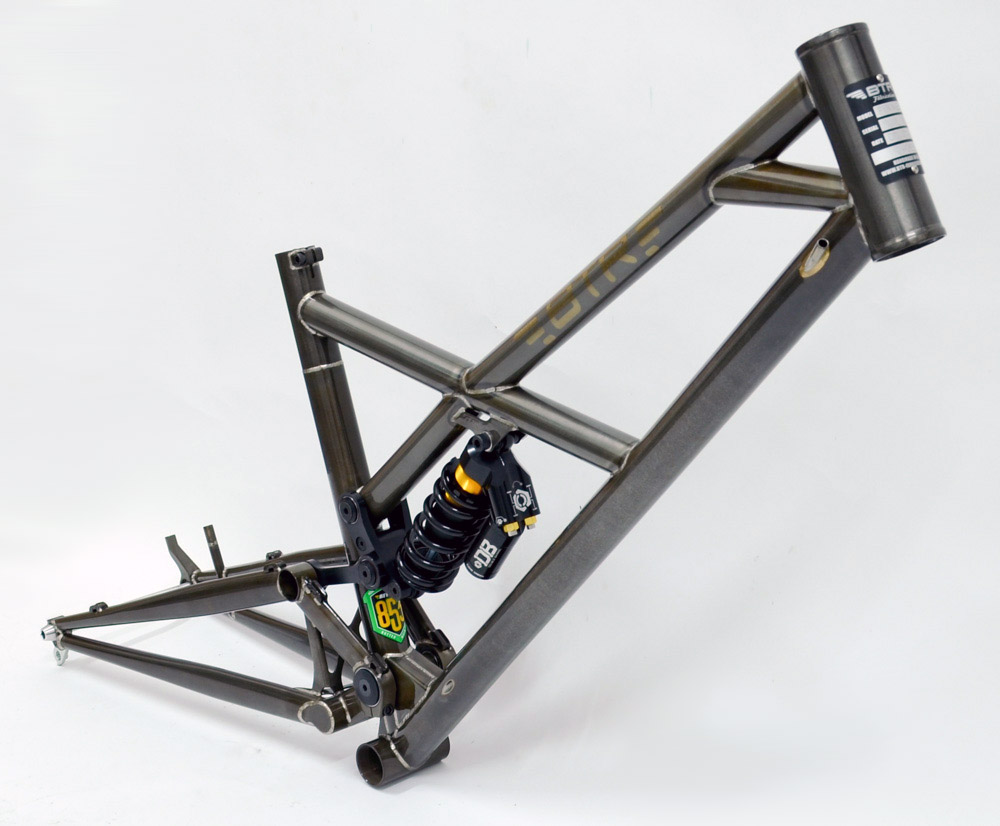
Morph Cycles is a new brand on the UK scene, and owner Tom Bugler has some warranted stoke for Reynolds tubing.
“A huge thing about being in the UK is that we have Reynolds based here, which is absolutely top quality tubing. It’s the best you can buy basically, and Reynolds brings a bunch of credibility with it. You’re building from top-quality proven tubing that builds really good bikes.”
Bugler also mentioned that the customizability of steel frames lends them to lasting longer because they give the customer exactly the bike they want rather than the flavor of the minute. He’s opted to skip model names and annual colorways for the time being to get away from the idea that bikes expire and need to be replaced when the latest version is released.
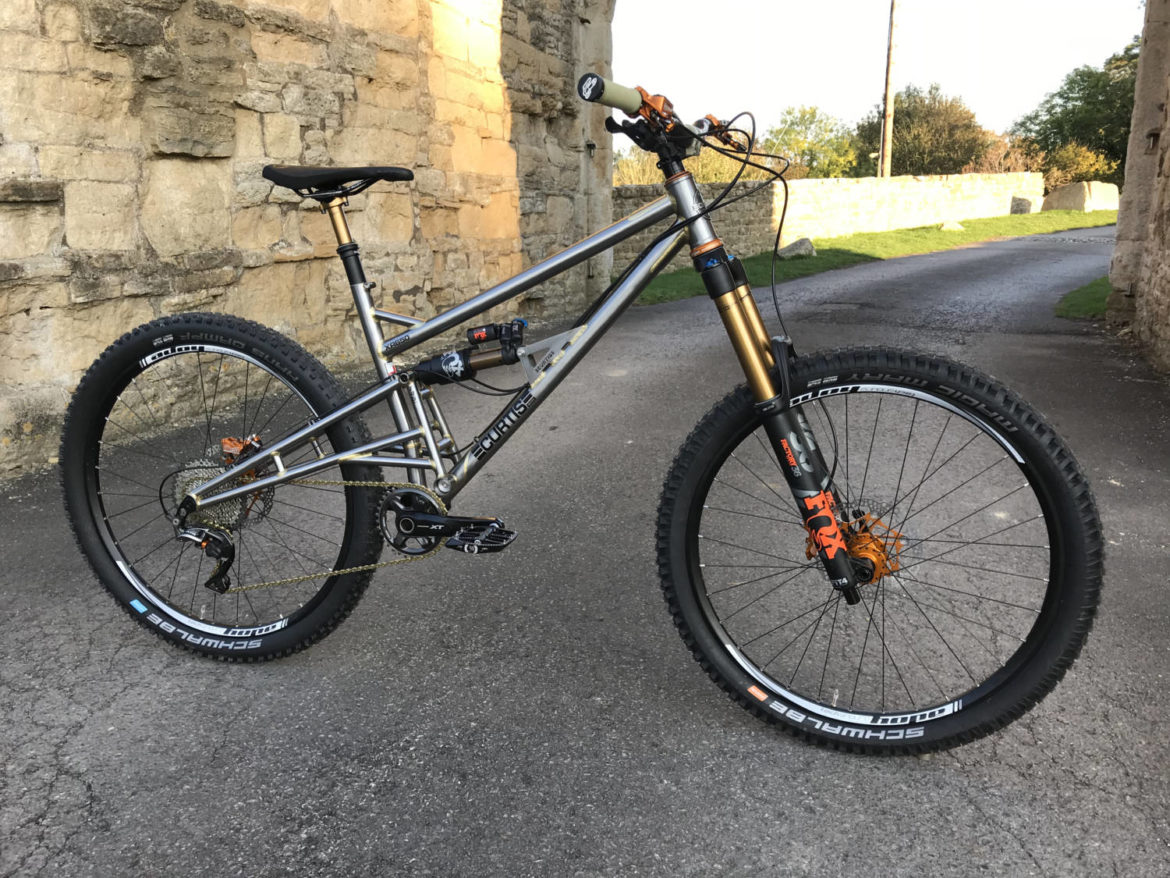
Finally, Damien from Production Privee has outlayed a clear and detailed narrative of the many benefits, durability considerations, and stress tolerances of steel tubing. One of the many important points concerning strength and durability is that “the fatigue strength is the ability to resist failure while undergoing cyclic loads. In other words, it’s a property describing the lifespan, the reliability. At this game, steel and titanium are materials of choice because under a certain stress level, their lifespan can be considered as unlimited. And that is not the case of an aluminum alloy which has a limited lifespan, shorter or longer according to the stress levels of the cyclic loads. Carbon composites have an exceptional lifespan only if their manufacturing processes are from an outstanding level (aerospace and defense industry levels).”
In case you were wondering how hard these modern steel frames can be ridden, we’ll leave you with this Pinner video from BTR Fabrications.
What’s your take on steel full suspension mountain bikes?
4 Comments
Apr 21, 2020
Nov 11, 2024
Mar 16, 2020
Nov 11, 2024