Industry Nine occupies a unique position in the world of mountain bike components. Not only do they engineer, design, and market their products from their US office, they actually manufacture them in Asheville, North Carolina. What began as a niche brand has grown tremendously–40% per year since 2013, in fact. Industry Nine’s (I9) hubs will always skew towards the boutique, but they are now a more common sight out on the trails thanks to wider distribution, additional price points, and new partnerships. Reynolds now uses I9 hubs on their wheelsets, and companies such as Santa Cruz and Ibis are offering them on certain builds.
I recently had the chance to visit I9 to see what it takes to make hubs in the US.
The Past
Many of you have likely heard the story of how Industry Nine got its name, but it makes for a good story, so I will tell it again. It comes from the fact that the hub and wheel business was the ninth industry–or company–started by owner, Clint Spiegel. Some of the companies that Clint started were successful and ended up being sold off, others did not fare as well. But how did Clint ever choose to manufacture cycling components in the first place?
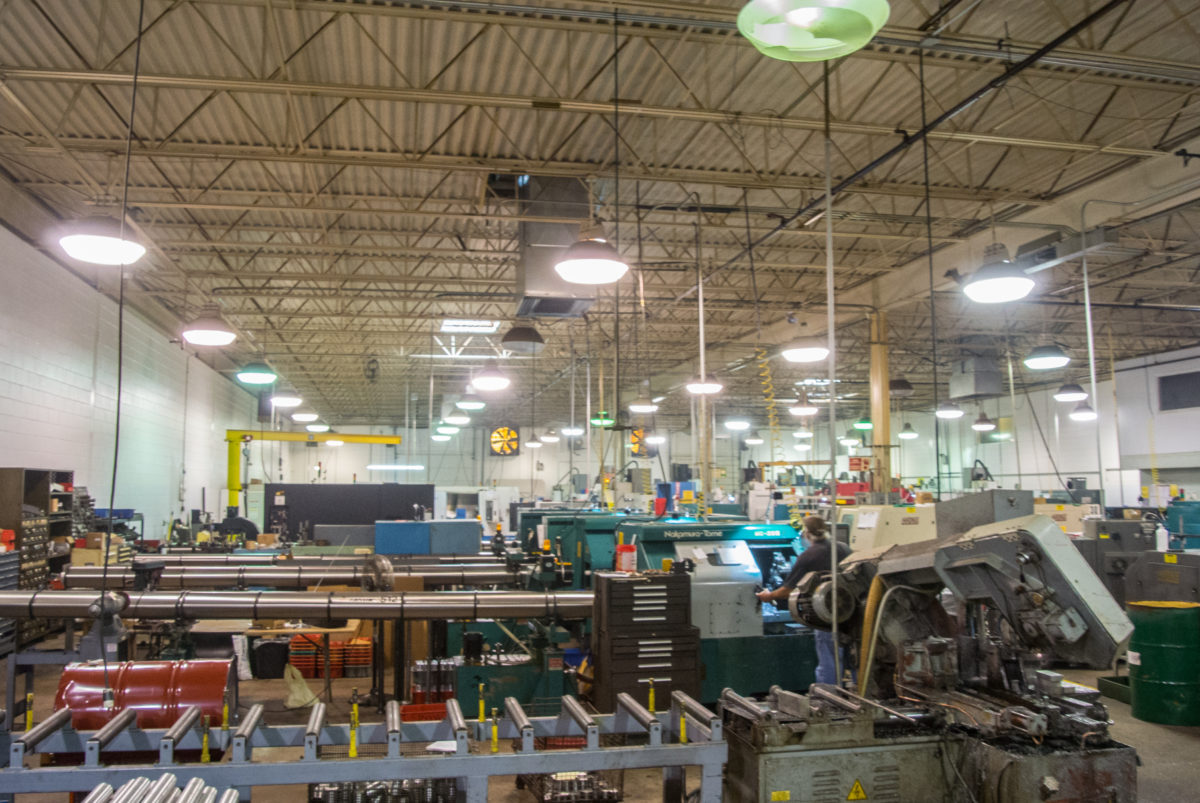
Clint grew up working in Turnamics, his father’s machine shop. Turnamics is a contract manufacturer that works on a variety of projects across numerous industries. By age 16, Clint was helping to manage the shop. After finishing college in the early 1990s, Clint returned to a company in trouble. More and more, companies were turning to overseas manufacturing–China in particular–to cut costs. In an effort to keep a steady stream of business going, Turnamics started to develop its own products. Their contract-based business did not dry up entirely, though. Some of the companies they worked with during those times included RockShox and Cane Creek.
Fast-forward to the early 2000s, and Clint was in his mid-30s with a couple of kids at home and was working too much. Deciding that he needed to get into shape, he started riding. On the bike, Clint started thinking about ways to improve the hub. After numerous ideas were tested, Clint settled on the drive mechanism and aluminum spokes that I9 still uses today. He debated on whether to license the design to another company, but in the end, he decided to manufacture his design in house.
The Present
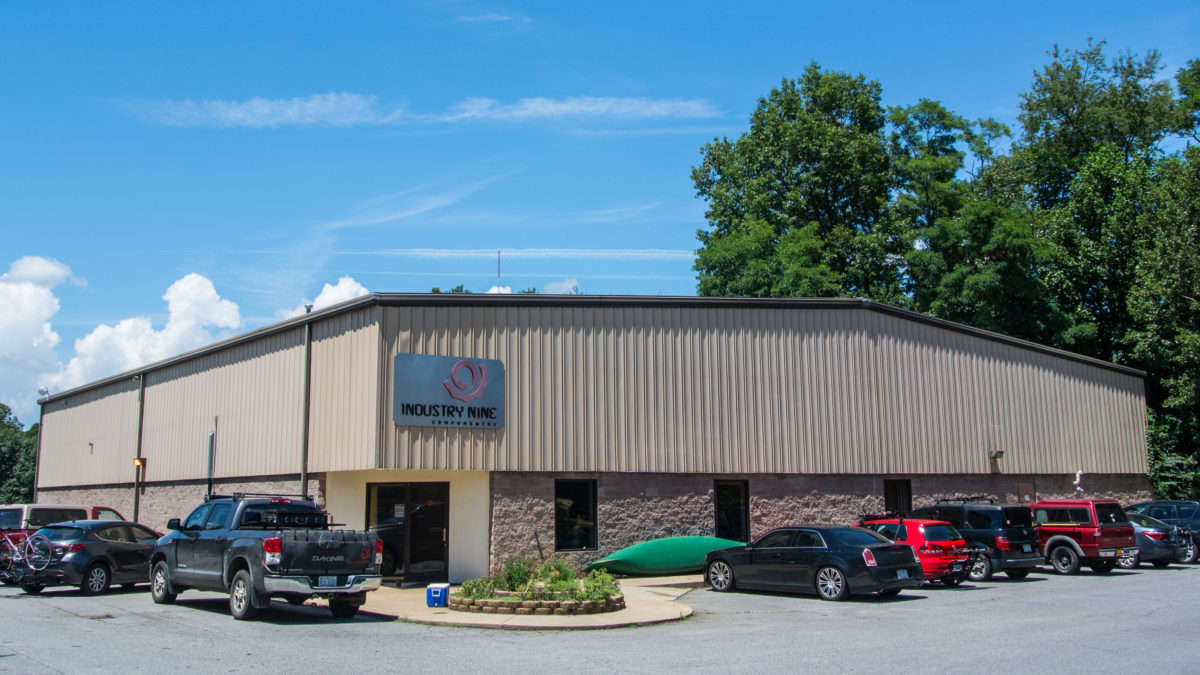
Turnamics still exists today, but now I9 takes up at least half of their manufacturing capacity in terms of operators and machines. As I9 continues to grow, that will only increase. Currently, I9 employs 35 people itself, while Turnamics employs another 40. So, in all, 55 people are involved with the wheel business.
Industry Nine’s headquarters sits on a hill just above the Turnamics machine shop. Inside the beige brick and corrugated metal building, their growth is apparent. No one here gets their own office. Even Clint the owner shares an office with Jacob McGahey, the Operations Manager. Jacob is as friendly as they come, but he is a fierce competitor. Look at the results from just about any race in Western North Carolina, and you will likely see his name near the top. While not technically an engineer, Jacob knows what works through practical, hands-on experience through years of racing and wrenching on bikes. In addition to managing people and inventory, he also designs their rims.
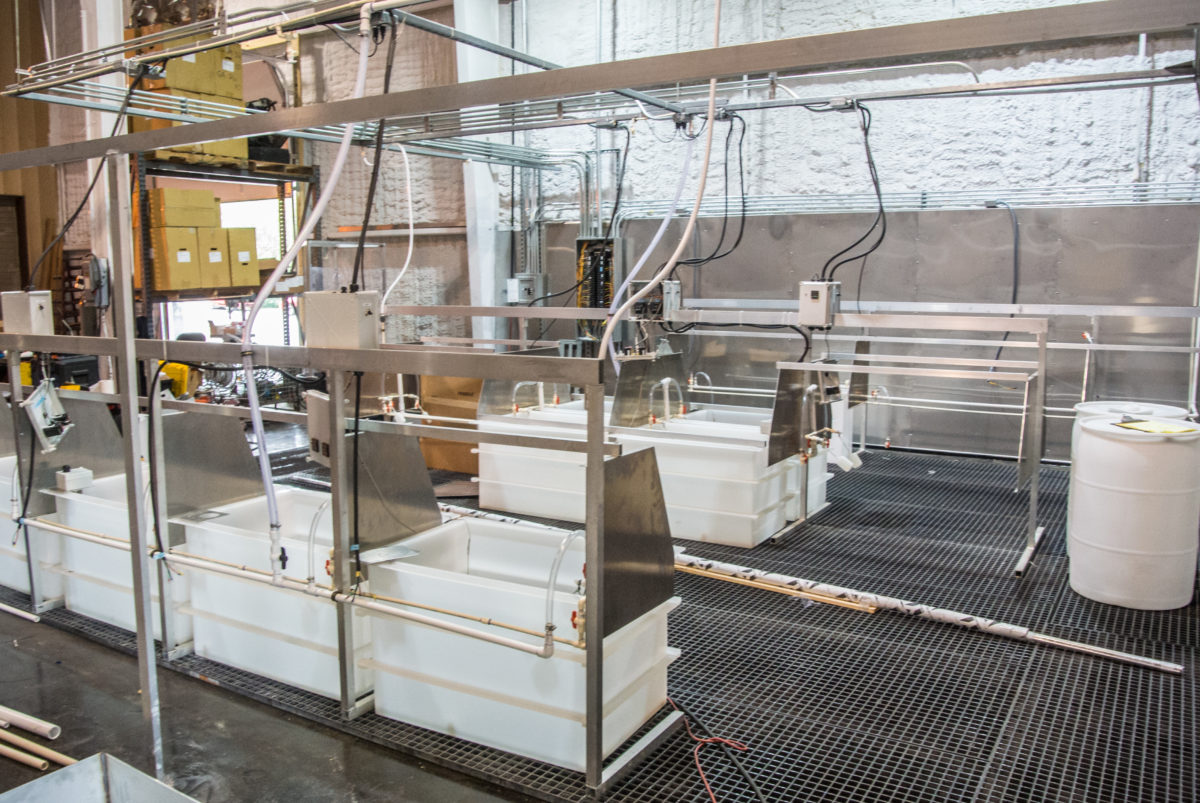
Jacob took me on a tour of their offices as well as the machine shop. Our first stop was their new anodizing area. Industry Nine has been doing their own anodizing for years, and they are known for the rainbow of colors they offer on their hubs and spokes. When ordering a custom set directly from I9, the only limit is your imagination. Anodizing is a tricky process since you have to control all aspects of it carefully. If not, you will end up with slightly different colors from batch to batch.
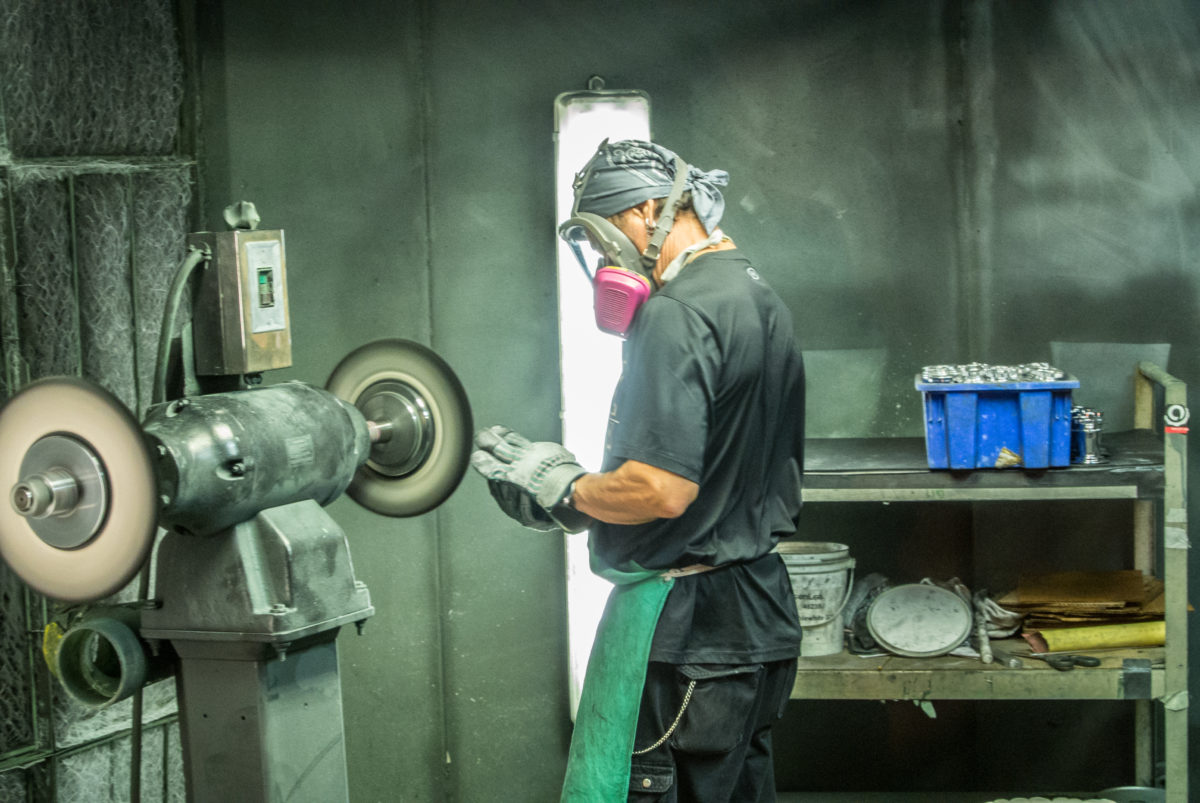
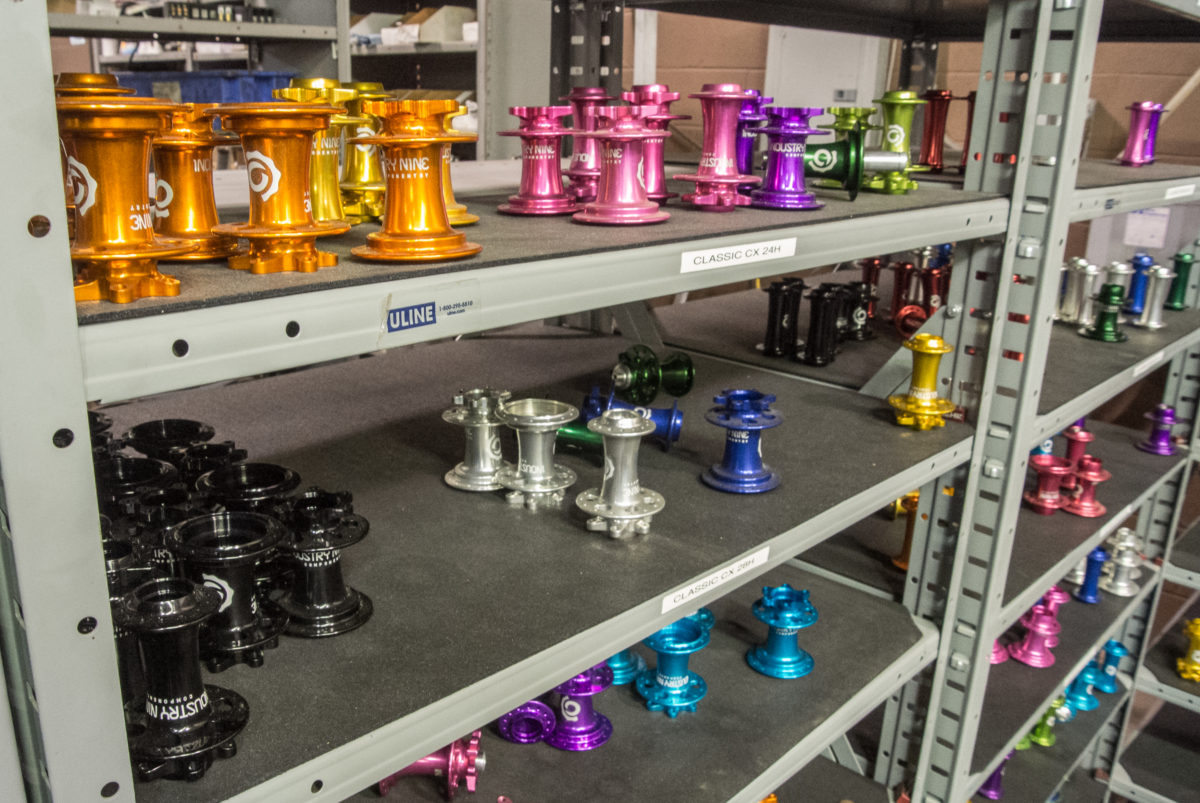
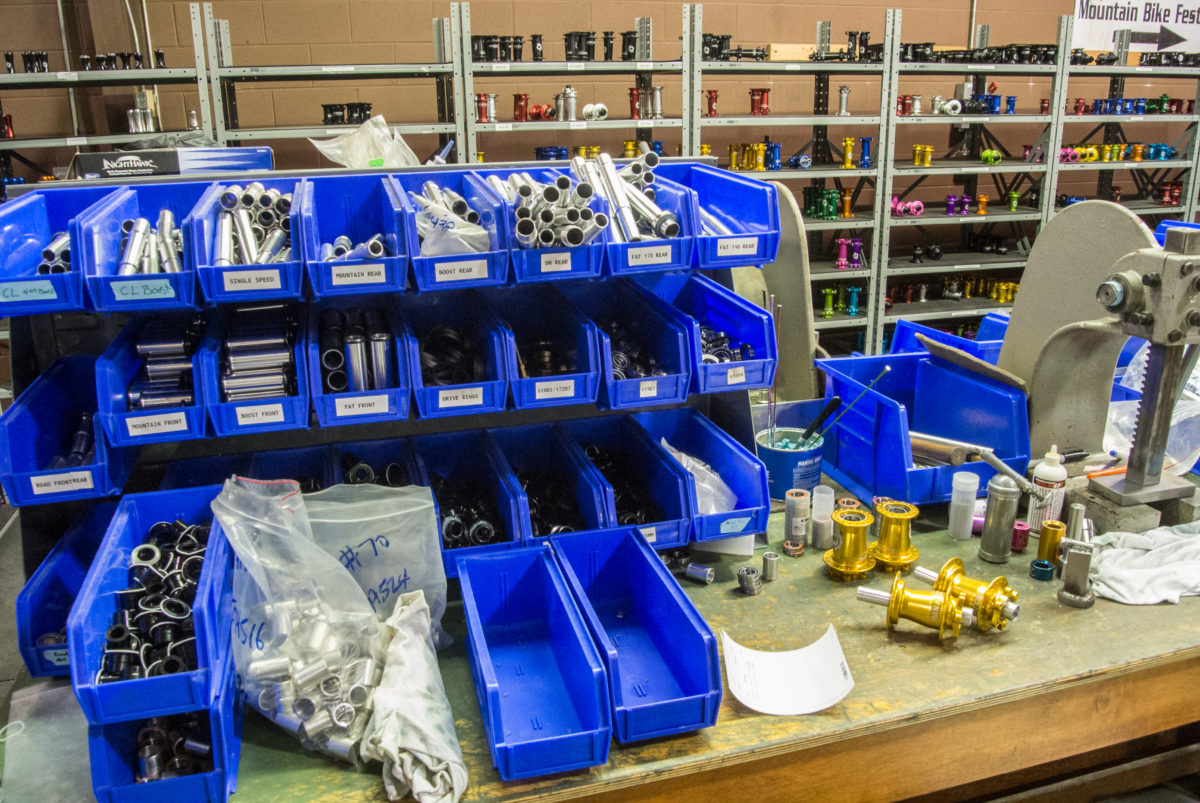
There were boxes of wheels stacked 20 feet high in the warehouse. Jacob said they aim to have a six-month stock of wheels on hand. Shelves upon shelves of brightly-colored hubs and aisles of spokes wait to be assembled into complete wheels. One large room is dedicated to wheel building, where several employees sit behind truing stands. They were working on all sorts of builds, from fat bike wheels to road disc.
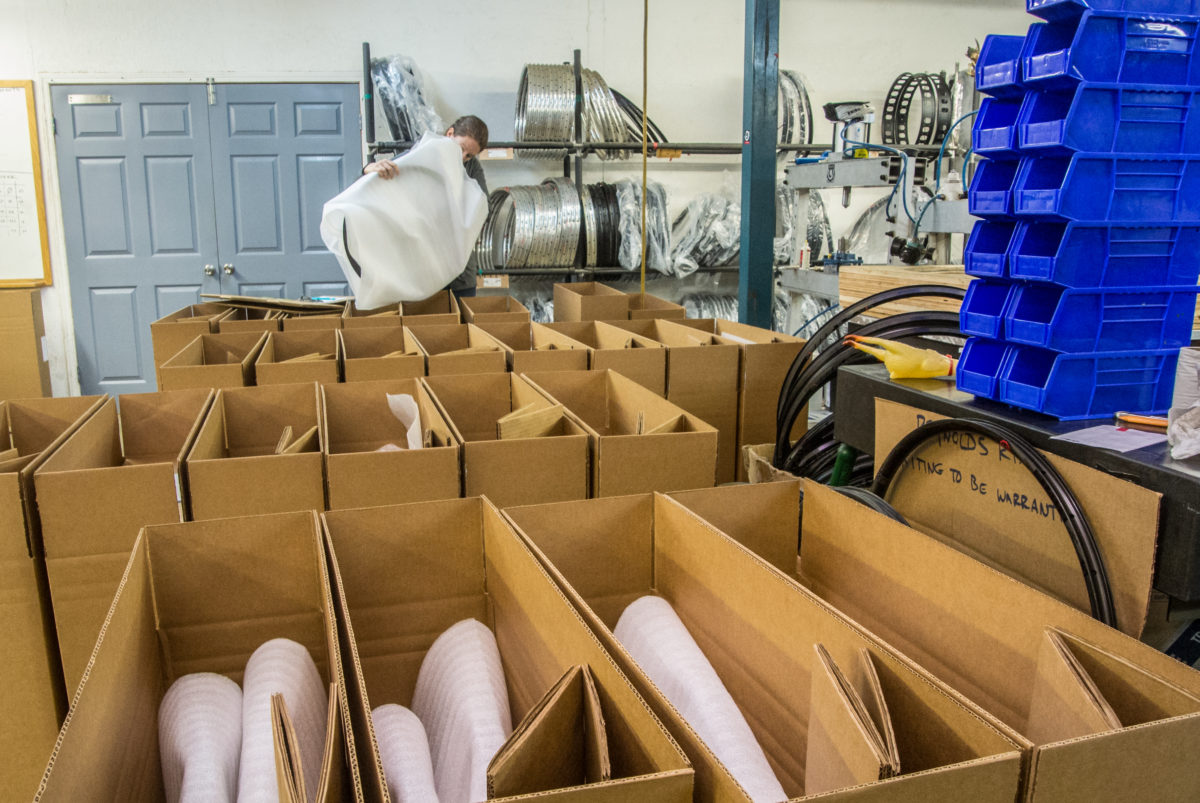
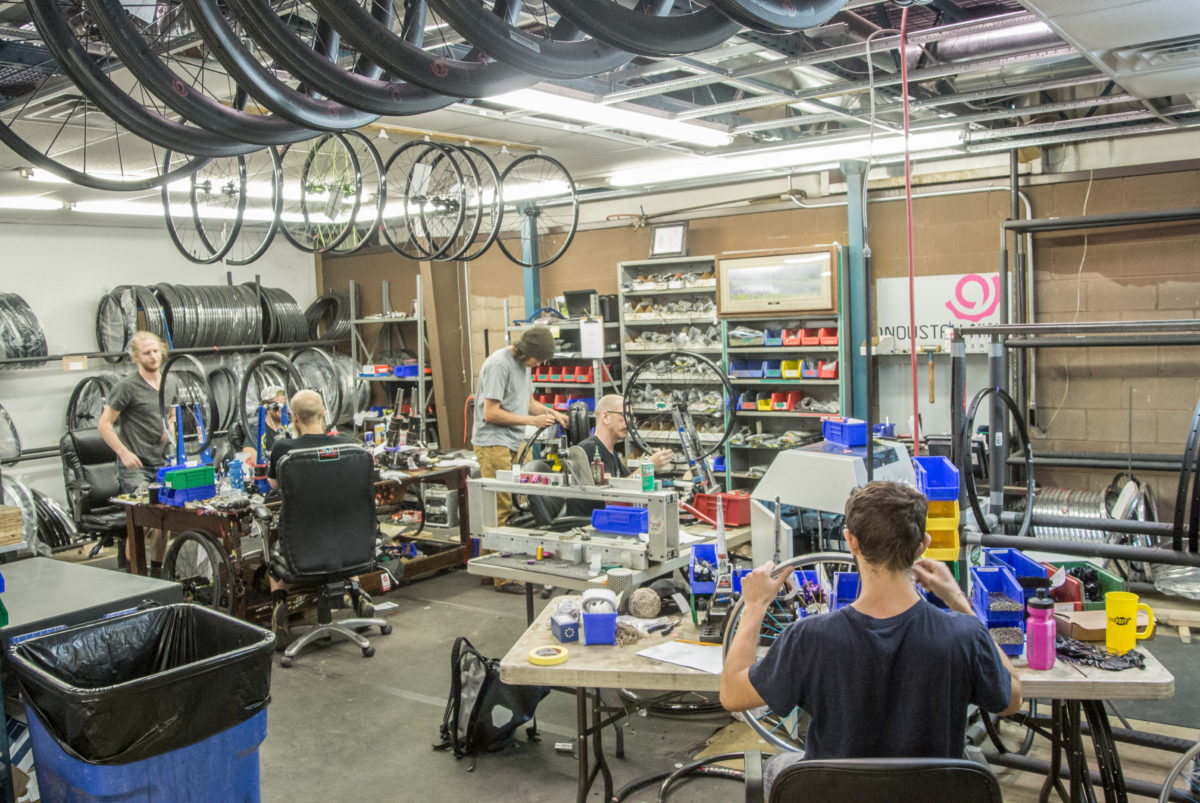
Of course, there is a pumptrack out back for Friday evenings.
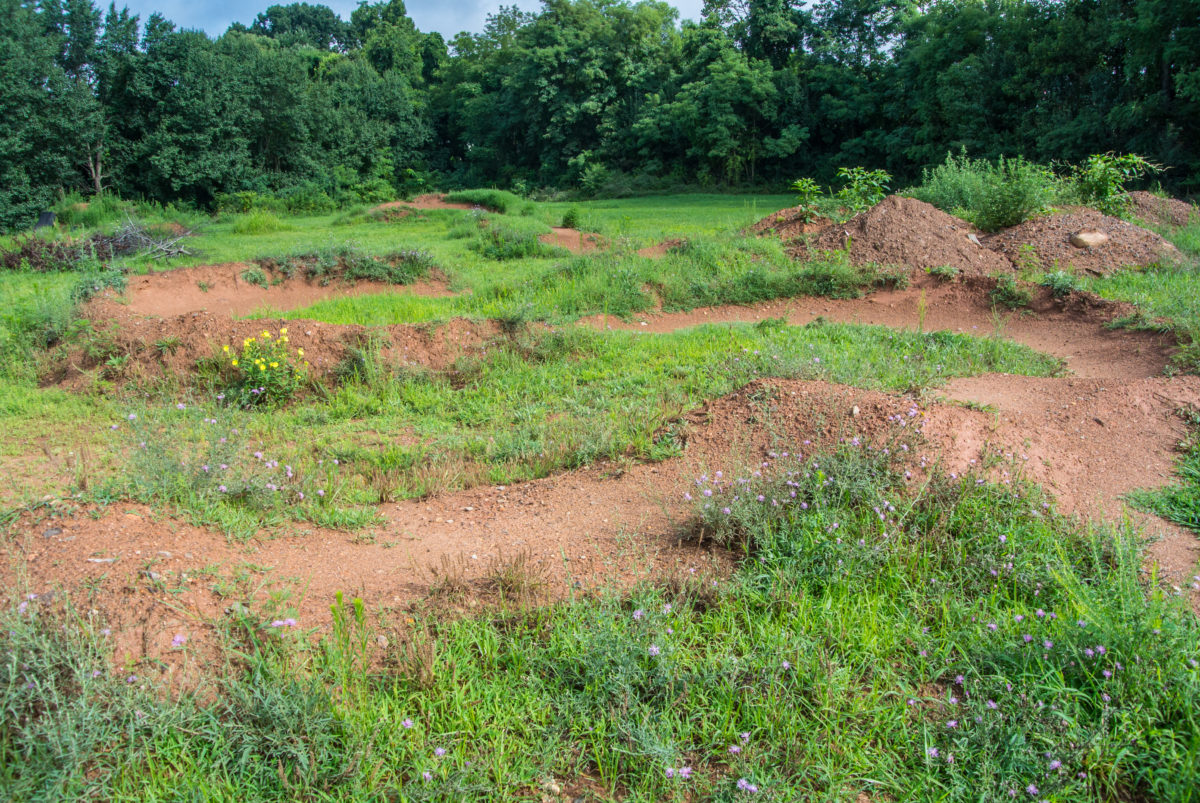

Down the hill in the machine shop, dozens of huge machines whir away, trimming down bar stock into hub shells. It’s loud, messy, and smells like oil–my kind of place. Jacob walks me through the rest of the shop, showing me the various steps in machining. We pass laser etchers and wire EDM machines. No, not electronic dance music–rather, electrical discharge machining.
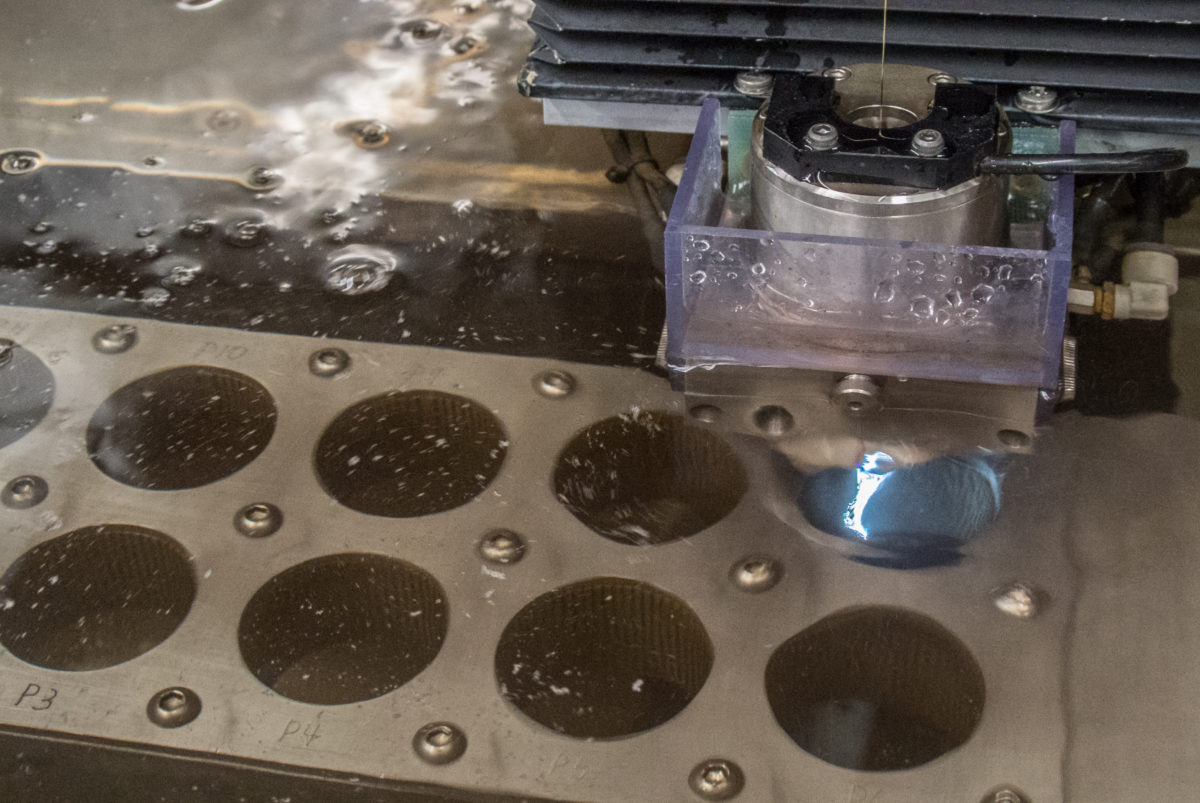
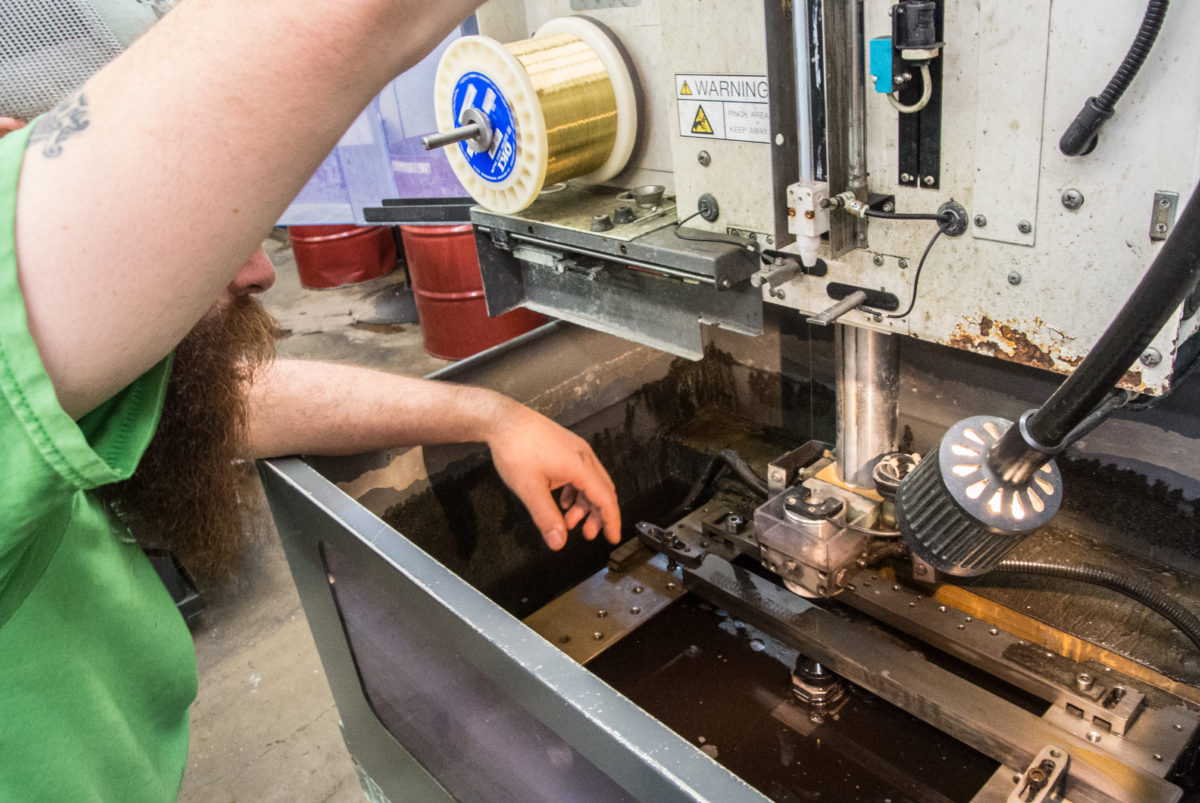
Industry Nine uses these machines to cut the drive rings and pawls that go in the hubs. To make them durable, the steel has to be heat-treated. However, if you tried to heat treat the final product, it would warp. So, the steel gets heat-treated first, and then the components are cut out of it. The steel is so hard, an EDM machine is the only way to cut them. Even with the machines, it is a long process. Cutting 60 of the drive rings takes a full 24 hours. This level of manufacturing and precision is what you are paying for when you purchase a set of their hubs.
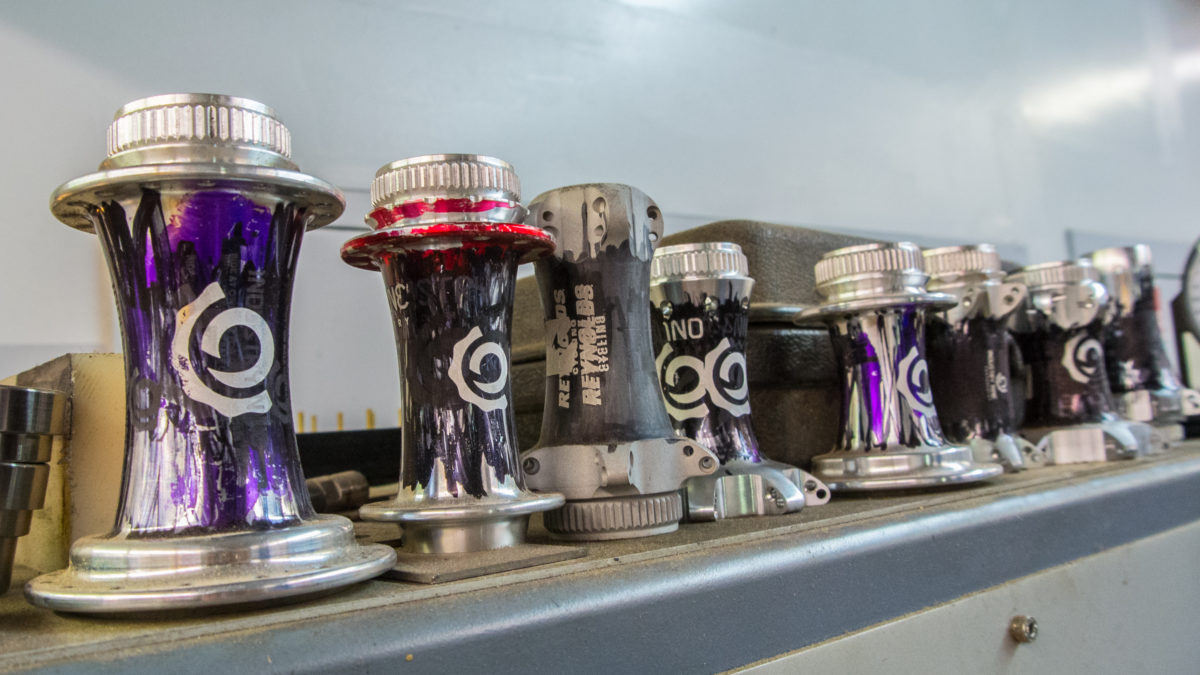
Other interesting machines on the tour include their laser etcher, which they use to add their logos to the hubs and spokes, and the spoke milling machine itself. Each spoke takes about a minute to machine. Six of these $350,000 machines are running at all times, cranking out spokes.
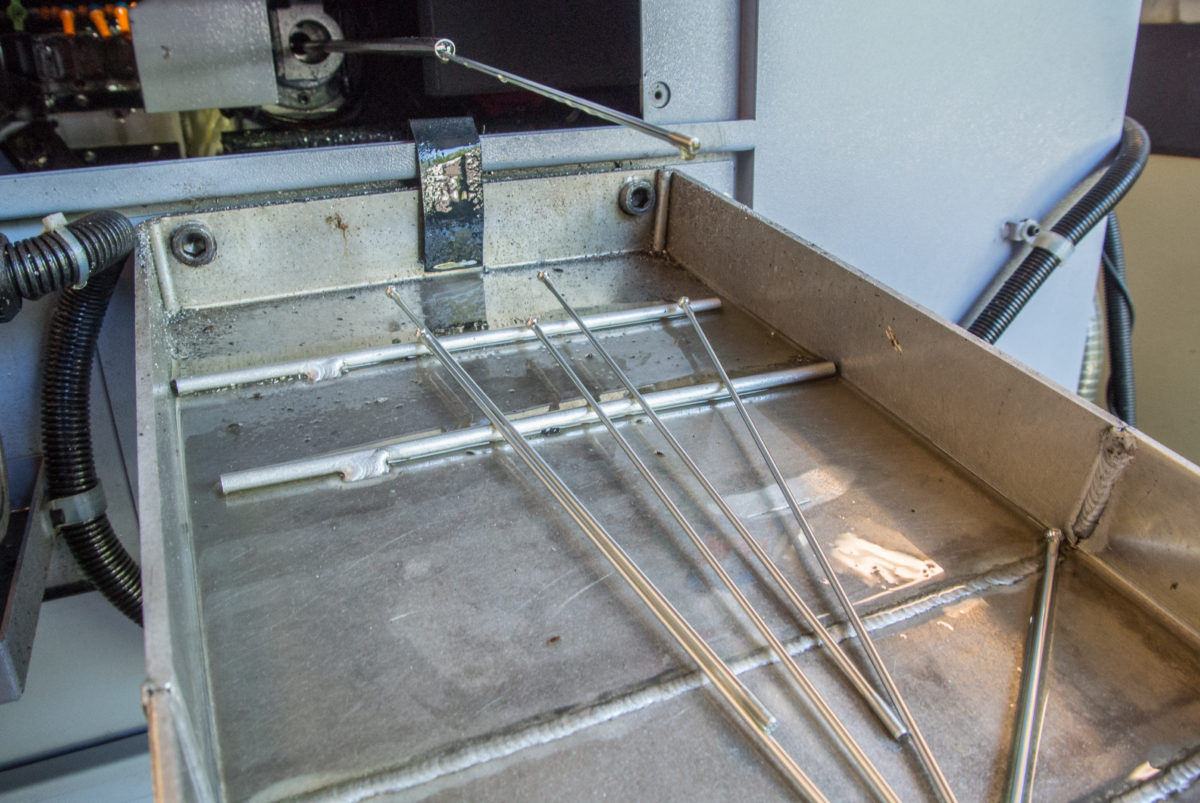
The Future
After talking to Clint, Jacob, and other employees, I got the sense that the company as a whole feels confident about the direction they are headed. Their growth in recent years has been substantial, but it was built on a solid foundation. Talk to anyone that owns a set of I9 wheels or hubs, and they will likely tell you they would never buy anything else. Should you ever have an issue with their products, a call or an email are all it takes to get it resolved.
Without a doubt, they have impressive manufacturing capabilities. And since Turnamics works across such varied industries, Industry Nine is always getting fresh ideas. The notion of a company called Industry Ten seems highly unlikely.
Thank you to Clint Spiegel and Jacob McGahey for the tour and conversation. Also, thanks to Jon Cartwright for riding Squirrel Gap in the pouring rain with me!
More Photos
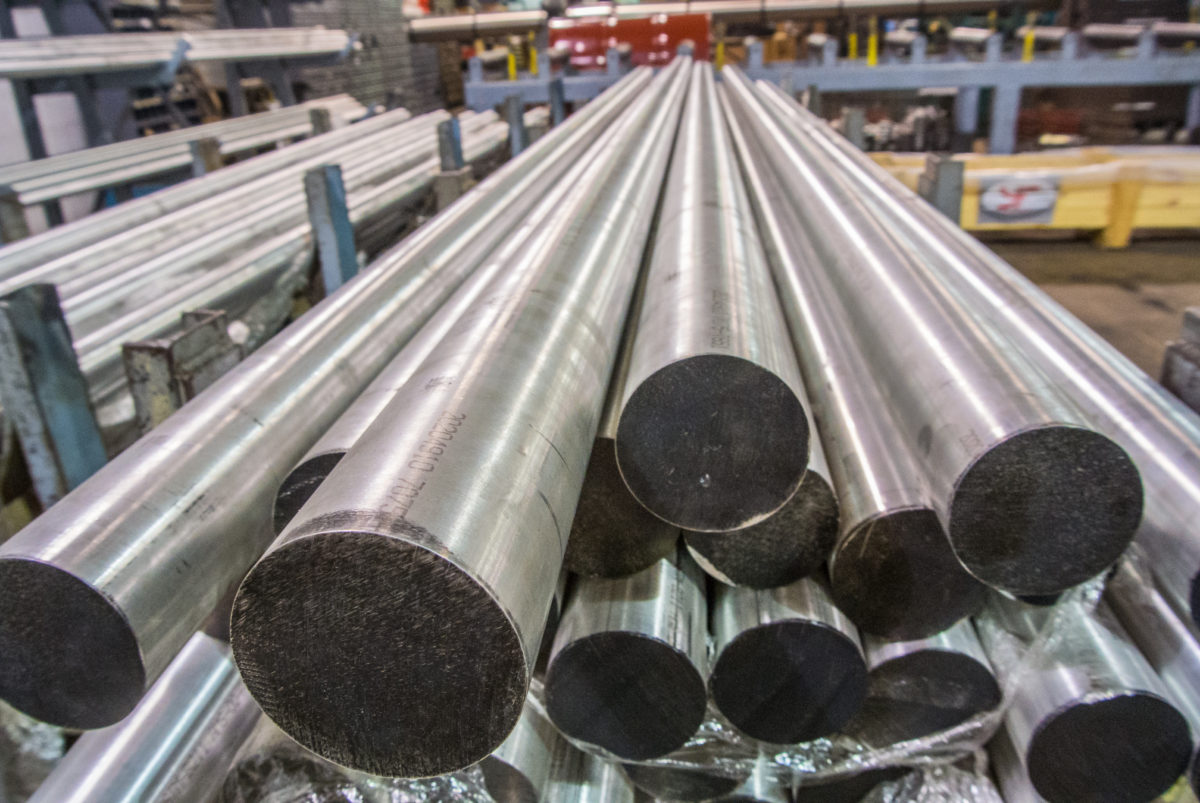
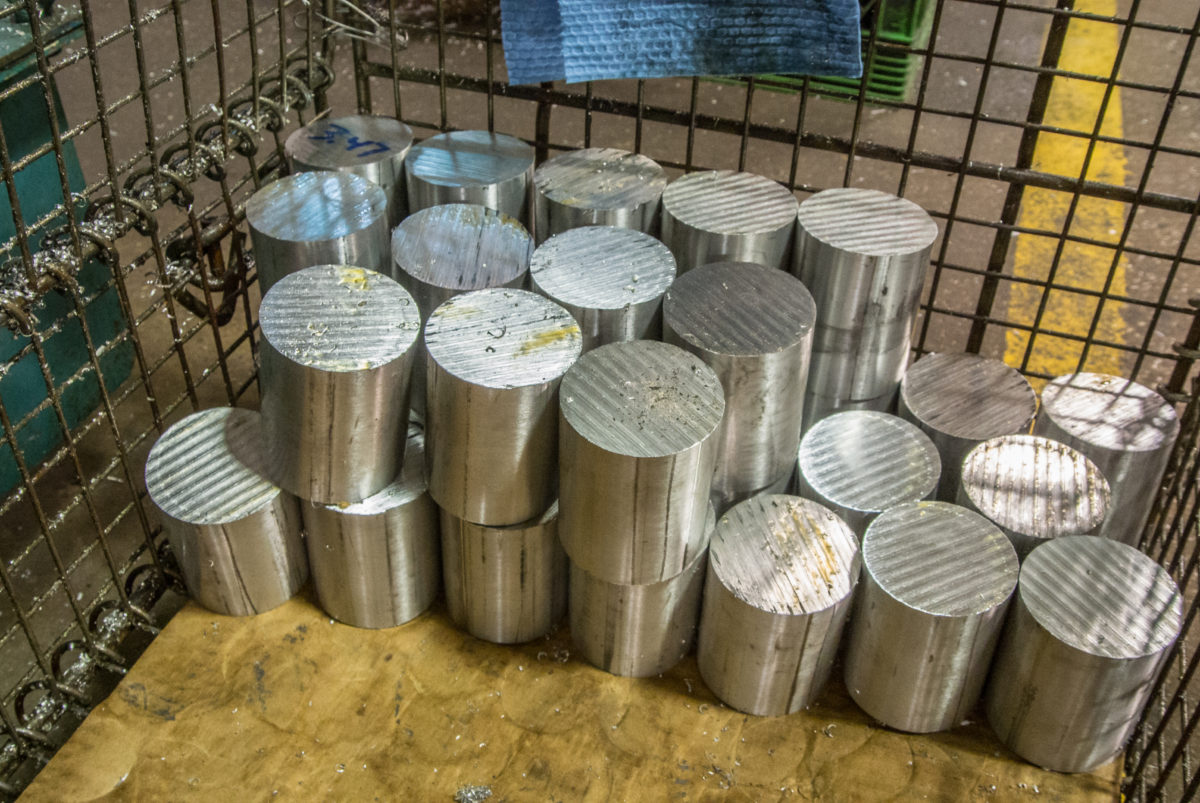
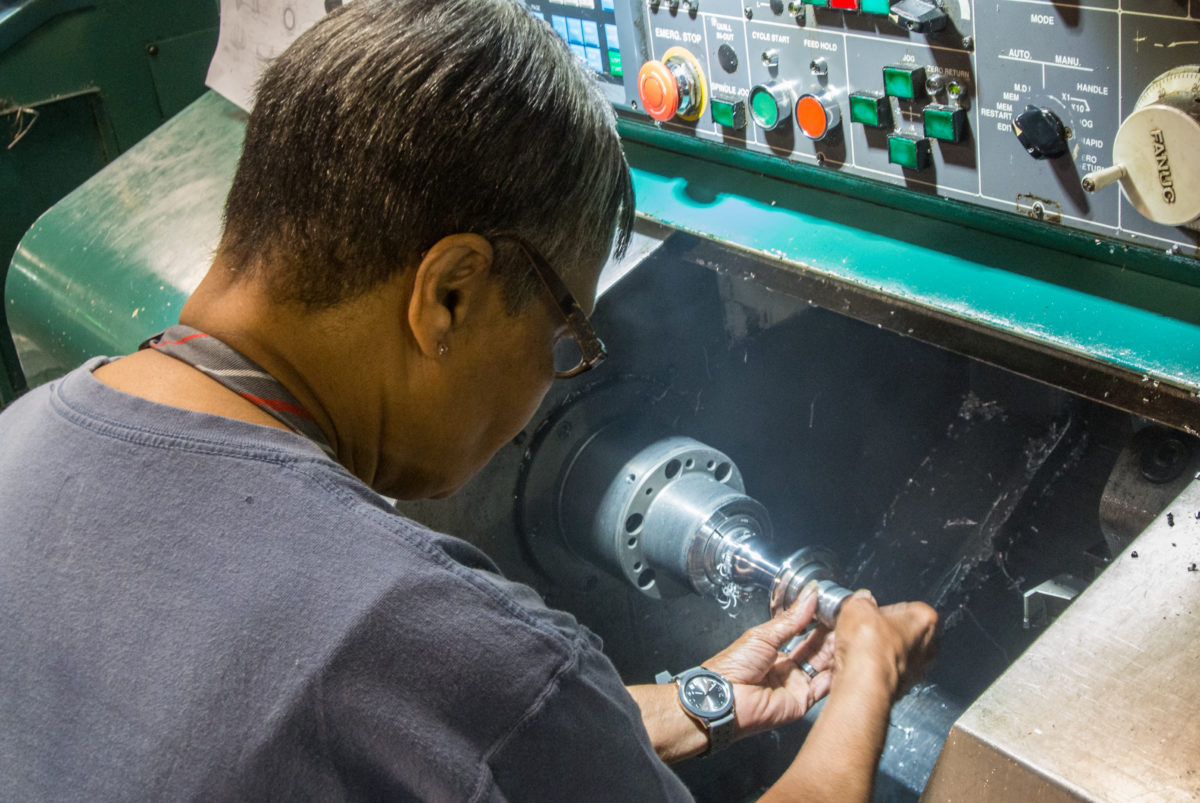
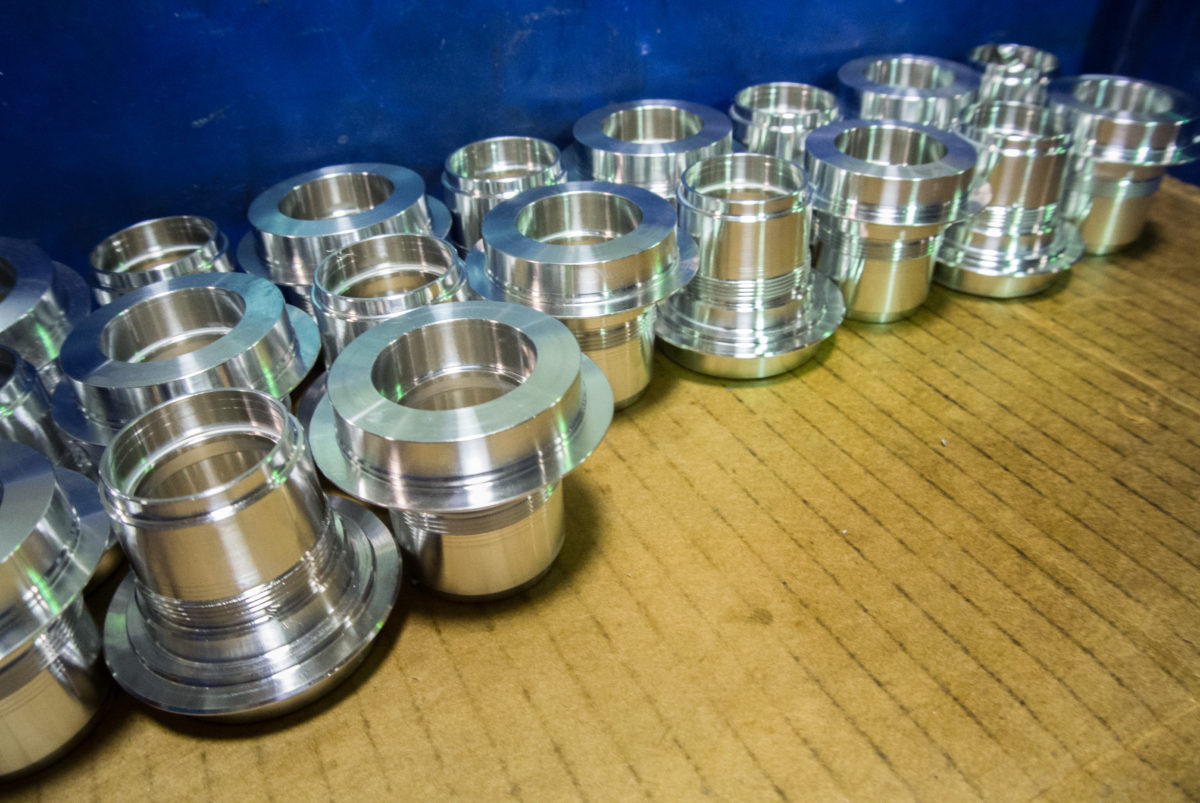
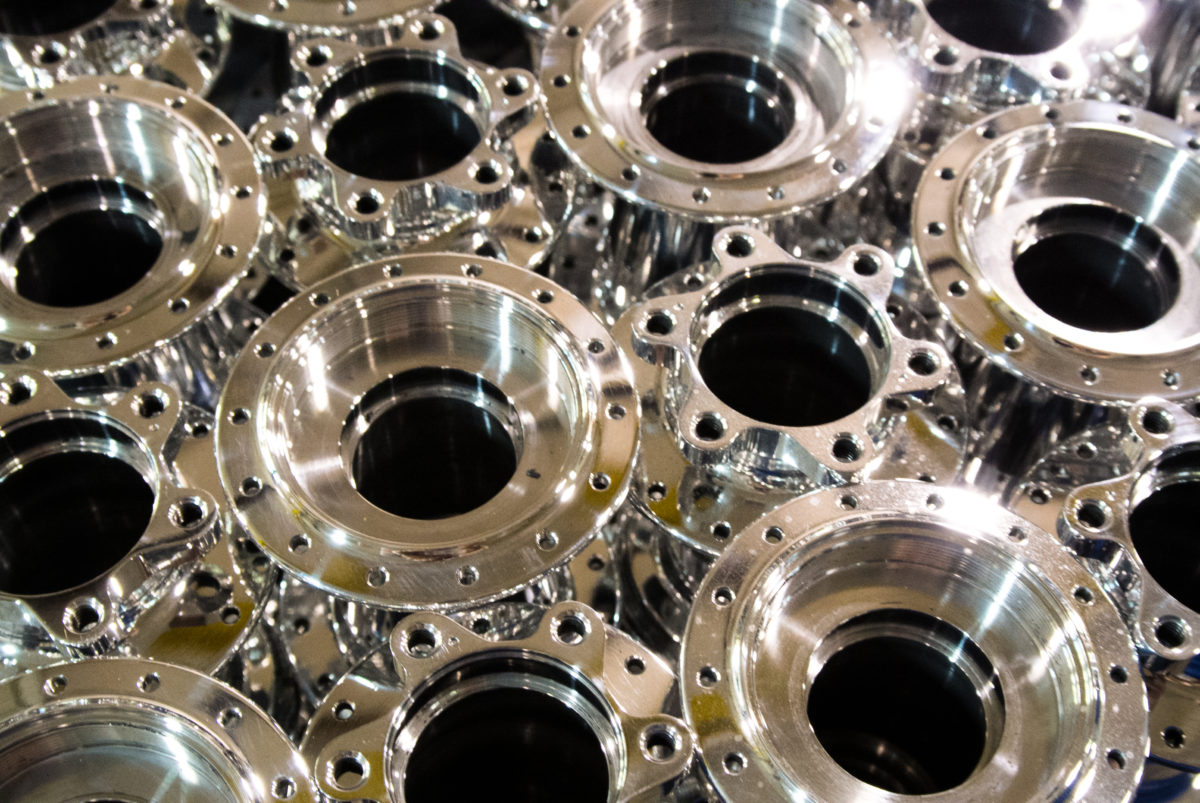
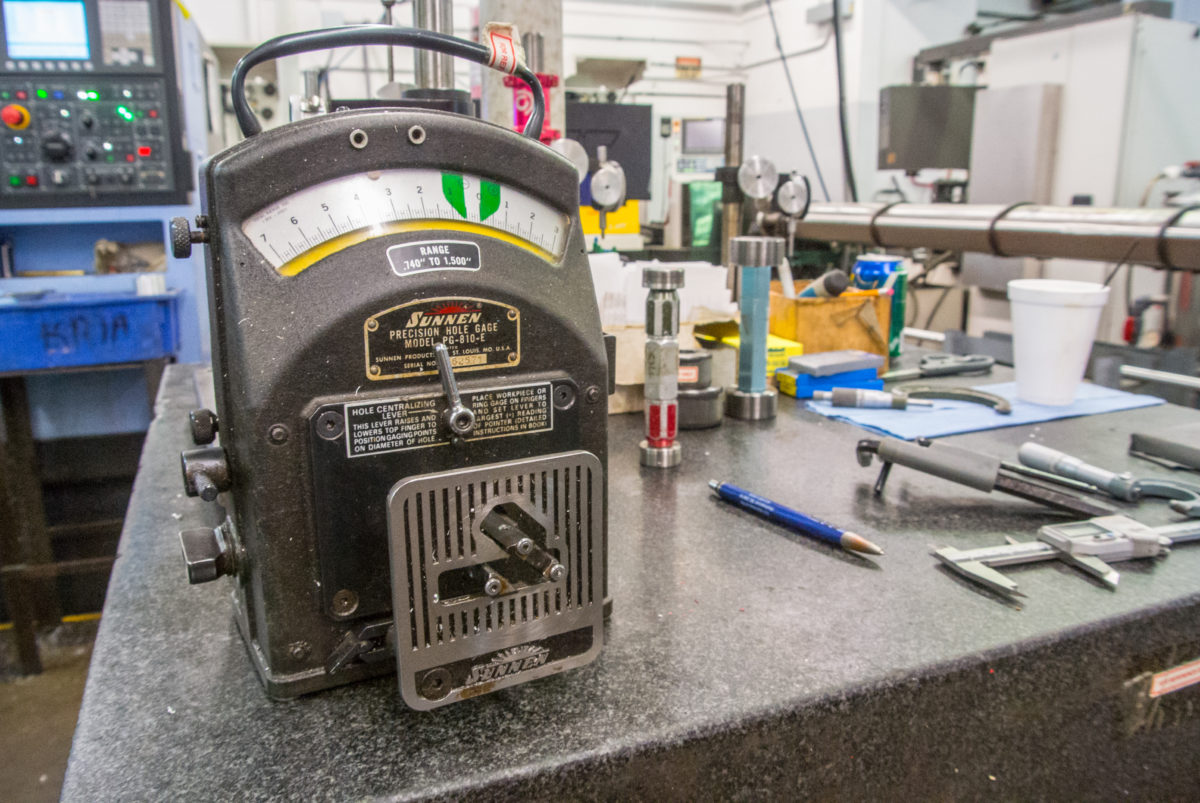
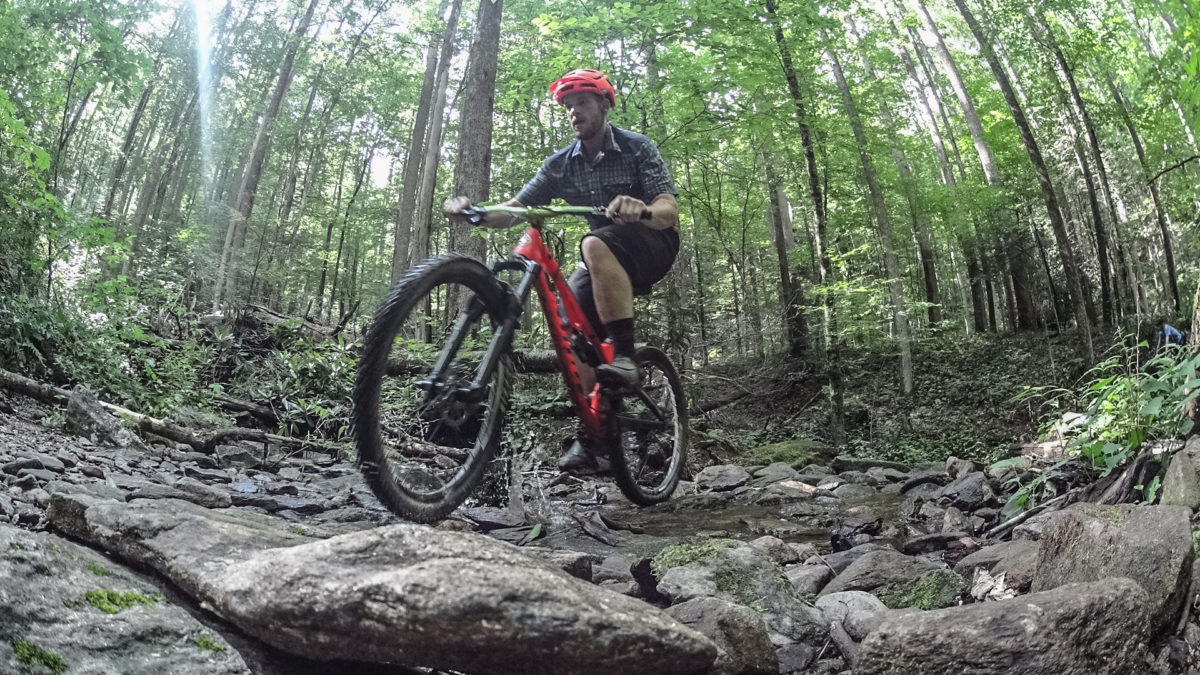
1 Comments
Sep 14, 2016